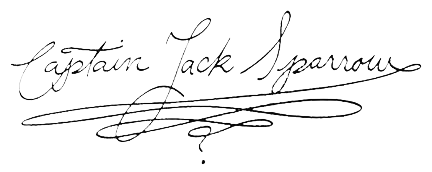
Venture below for the forum of The Brethren Court!
If you would like to add information or you find dead links to pictures or sites please send an email to the administrators
Venture below for the forum of The Brethren Court!
If you would like to add information or you find dead links to pictures or sites please send an email to the administrators
Sash Tutorial
* Since the creation of this tutorial - I have bought an ACME sash and firmly believe that is the way to go. You can't even find an IKEA curtain anymore - so this tutorial is practically useless. Contact ACME for a sash.
Tutorial by Mojo from brethrencourt.net
The rumor goes that the material for Jack Sparrow's sash comes from a village in Turkey, where it was woven by peasants. The filmmakers bought 50 yards for the first film and then had to go back to the village to get 100 yards for the subsequent movies. They decided to get more of the original instead of simply silk-screening the print because "it sheds and ages so beautifully," Penny Rose [costumer for the POTC movies] explained. "Plus, to keep the spirit of Jack Sparrow going, we'd better get the exact same thing!"
Well I started off thinking I could jont down to my local IKEA and pick up the sash fabric [aka "curtain"], when lo and behold they were sold out. They could not tell me if the pattern was discontinued, or when the next shipment was, they just stared at me and shrugged their shoulders. IKEA doesn't sell floor models, they don't do store to store transfers, they don't special order and you can't buy the curtain off the web. So adopt this rule when you are shopping for anything: If you see it - buy it. But this tutorial will work for ANY fabric that you find. As of this writing the IKEA fabric is sold out everywhere and the only way I have been able to find it since is on ebay and other auction sites.
The curtain from IKEA is called Alvine Smal and is a very close pattern to Jack's sash from Curse of the Black Pearl.
This is what it looks like out of the wrap:
Getting Ready: The first thing that I did was take a seam ripper to all the seams and "curtain-y" things and separate the scrap from the bulk of the item.
I even pulled out every seam - on every scrap and panel so that the only thing I was left with was just fabric. Then I threw everything in the wash cycle with some oxy-clean and ran the load twice.
Let me just say, the material without the hem is very thread-y. I could have wound up all the loose thread and made a spool - so be prepared for "spider-webs."
Measurements: The next thing I did was decide how wide to make my sash. My first sash was a costumebase brand and was 14" wide.
I think a wider sash works when you have a shorter "length" sash. But the longer your sash gets, the shorter in width you can make it. You have to take into consideration how many times the sash gets wrapped around your waist. My original sash can only wrap around my waist one time because it is only a little over eight feet and I needed some material to hang down to my boot. But a thinner sash will reduce the amount of fabric wrapped around you [and thus reduce bulk].
So I am deciding to make my new sash 11" wide and close to 16 feet long. (with these dimensions you can make 5 sashes from one pair of curtains). Sixteen feet is almost exactly how long two curtain panels are end to end. So I lined up the two panels and found sections in each where the pattern "lined up" and then measured off 11" with a ruler and a pencil and made a "notch" cut with a pair of scissors.
If you make a small notch with the scissors in the end of the sash, you can hand rip a "line" all the way down the fabric. I made sure that I took a piece from the inside of the curtain, that way both the top and bottom of my sash have the same "ripped edge." So when it lines up, it should look the same.
Next I found an acceptable pattern that lined up with two of the panels and ironed both ends. We then tested two different ways to stich them together. The first was overlapping -the two sashes were "end to end" and overlapping 1/4 inch] and we ran a stitch down the overlap. [we didn't like it]. The second way was flush - the two sash ends panels were flat on top of each other and we stitched a line going through them both [the way you would make a seam] - and that's the one we liked. This is important sew your material together before you begin washing or weathering. The fabric is stiff and flat and this is the perfect time to get it under the sewing machine.
When we were folding the material up for the night, my wife commented how "stiff" it felt and I remembered there were some sash designers who had said that they "softened" theirs. Turns out a common way to not only set dyes and remove odors is to use a cup of white vinegar in a cold wash. So back in the washing machine they went.... this time I am going to try a low heat when I dry them.
Another option for softening fabric is to apply milk to the wash cycle or
To iron the clothes while they are damp or
To tumble dry the material with a pair of sneakers and
To store the material rolled up tight.
Suffice it to say all of that did...nothing. The fabric is still stiff and now I had more threads to break off.
We then tested the idea of making a "loop." we measured off a sizable peice [about five feet] and placed a "bar" of fabric in the middle of the sash [not the middle "end-to-end" - the middle "top-to-bottom."] seen in the picture below.
Weathering Holes: Then using Cap'n Neon's weathering tutorial and some key photo references, I used sandpaper to rough up the fabric, a screw driver to punch holes, a wire brush to fray the ends of the sash and a pair of dull scissors to "dress up" some holes and tears throughout the entire length of the sash. This is important though - make sure you make all your holes and ends BEFORE it gets wet. The tea water will help all the clean edge cuts fray up and then later after you stick it in the dryer - the heat will make all your cuts nice and rugged looking.
Weathering Color: Then I began to prepare the tea dying process. As the water was getting warmer and the tea was steeping, I soaked my sash in warm water. As with any dying process you should never lower dry clothes into any dye solution.
Going into the pot... I boiled it with 4 tea bags of Lipton [decaffeinated]
One of the things that I did - that I think is a good idea: I placed a few of the fabric scraps in the pot and occasionally took them out and dried them. That way I knew what the true color was periodically and I didn't have to wait for the whole sash to dry to find out.
So I ended up tea dying it for about 2 hours the first time and over 5 hours the second time. But I can see why some people do it longer or even for over night. 20 minutes is like a yellow fade, and not very noticeable.
...And if you don't believe it looks THAT weathered, compare it with a sash I have left unweathered.
After it came out of the dryer, I busted out my black spray paint and paint tarp and did the ends of my sash TK409 style and I think the whole thing turned out great. In the end, I probebly washed it in cold water five times [2x with vinegar], tea stained it twice and spray painted the ends when I was done to get it just right. (more weathered ref pics - 1 2 3) Sashes that I have done more recently got a streamlined process; I ripped, tea-soaked overnight, dried and then spray-painted. There are also theater quality paints like Dirty Brown and whole earth products that can help you get that weathered look. "Nobody likes a clean pirate."
Touch ups: I ended up remeasuring the width after I did a trial dress rehearsal. Regardless of what everybody "says" ultimately the sash needs to look right "on you" so length and width should be up to you and how it looks live and on camera. So I felt the width was a little much, I am only 5'5 so I can't have it cover a large section of my body or it will be "all sash." So I remeasured and cut the sash down the length by another inch. So right now my sash is 10" in wide.
The Completed Sash:
If you would like to add information or you find dead links to pictures or sites please send an email to the administrators